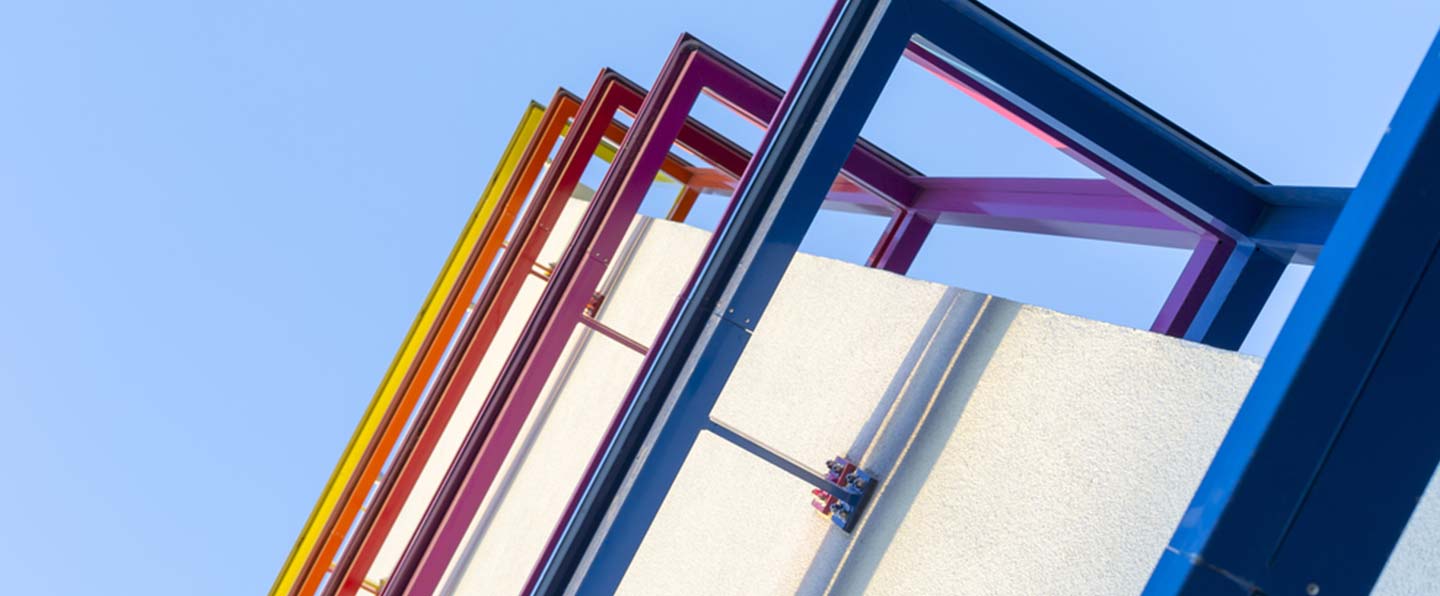
SUSTAINABILTY.
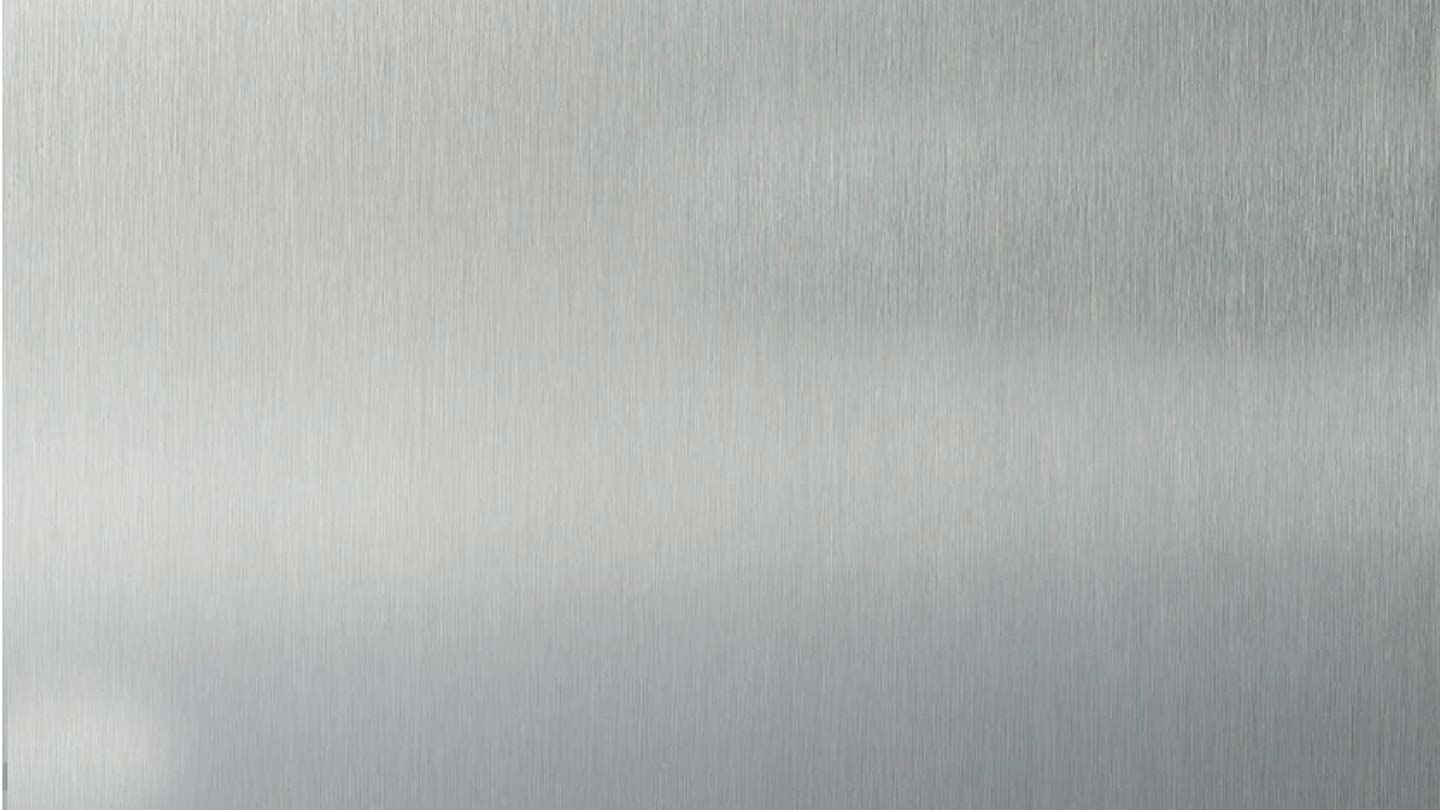
LINETEC ENVIRONMENTAL & SUSTAINABLE GREEN BUILDING
Linetec has a long-standing reputation as a leader in environmentally-conscious process improvements and sustainable design finishes and coatings.
The built environment has a profound impact on our environment, economy, health and productivity. Whether baking in the sun or freezing in the cold, building envelope endures some of the most rigorous, day-to-day durability challenges. Selecting an exterior architectural finish that will preserve the longest lifespan possible can be a daunting task.
Since the inception of LEED in 1998, the explosion of building green has increased awareness of the various finishing options and their performance criteria. The finishing technologies and processes involved in design, construction and manufacturing are extremely important to a building’s longevity and sustainability. The goals of environmentally responsible architectural finishing companies follow the same mission as the USGBC.
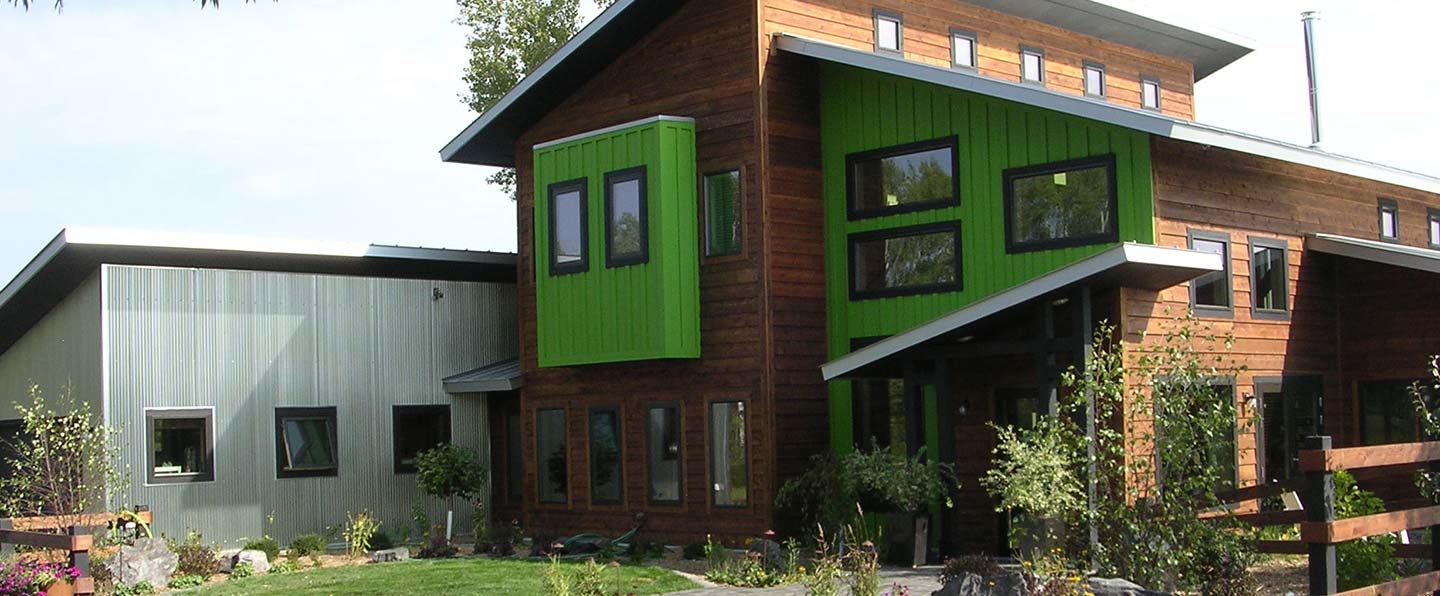
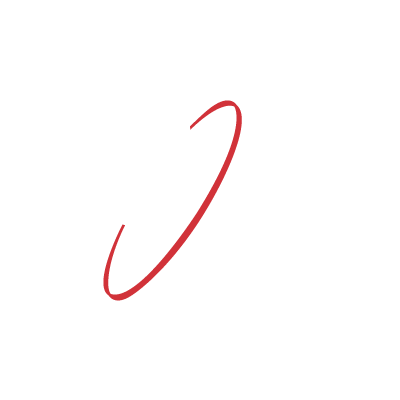
LINETEC AND USGBC’S SHARED MISSION:
“to transform the way buildings and communities are designed, built and operated, enabling an environmentally and socially responsible, healthy, and prosperous environment that improves the quality of life.”
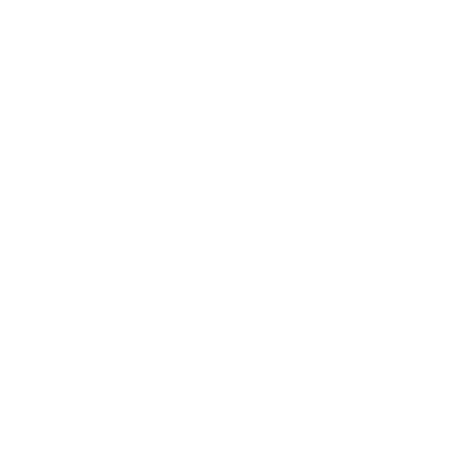
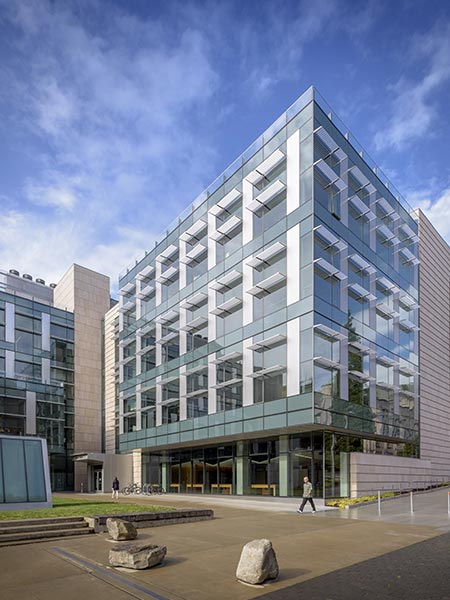
Environmental Protected Finishes
In the architectural and commercial industry, the three types of factory-applied, high-performance finishes for aluminum are polyvinylidene fluoride (PVDF) paint, powder coat and anodize. All three processes can be applied securely and permanently to the building’s aluminum components, with environmental protection inherent in the finish.
Applicator key to determining the best options
The finish choice most often is based on a combination of personal taste and performance specifications. Selecting the appropriate finish for the building’s exterior involves much more than just choosing a color. Conversing with an applicator that has experience with all three finish types can be beneficial in determining the best application for your project.
LEED IEQ CREDITS
Unless applied on site, architectural finishes do not contribute to the attainment of the LEED Indoor Environmental Quality (IEQ) Credit: Low-Emitting Materials – Paints and Coatings, but they most assuredly do contribute to the sustainability of a building.
reducing negative impact on environment
Selecting an applicator that supports green building finishing through ongoing research and environmentally-friendly business practices will help to significantly reduce negative impact on the environment.
eco-friendly finishes & Services
Selecting an applicator that supports green building finishing through ongoing research and environmentally-friendly business practices will help to significantly reduce negative impact on the environment.
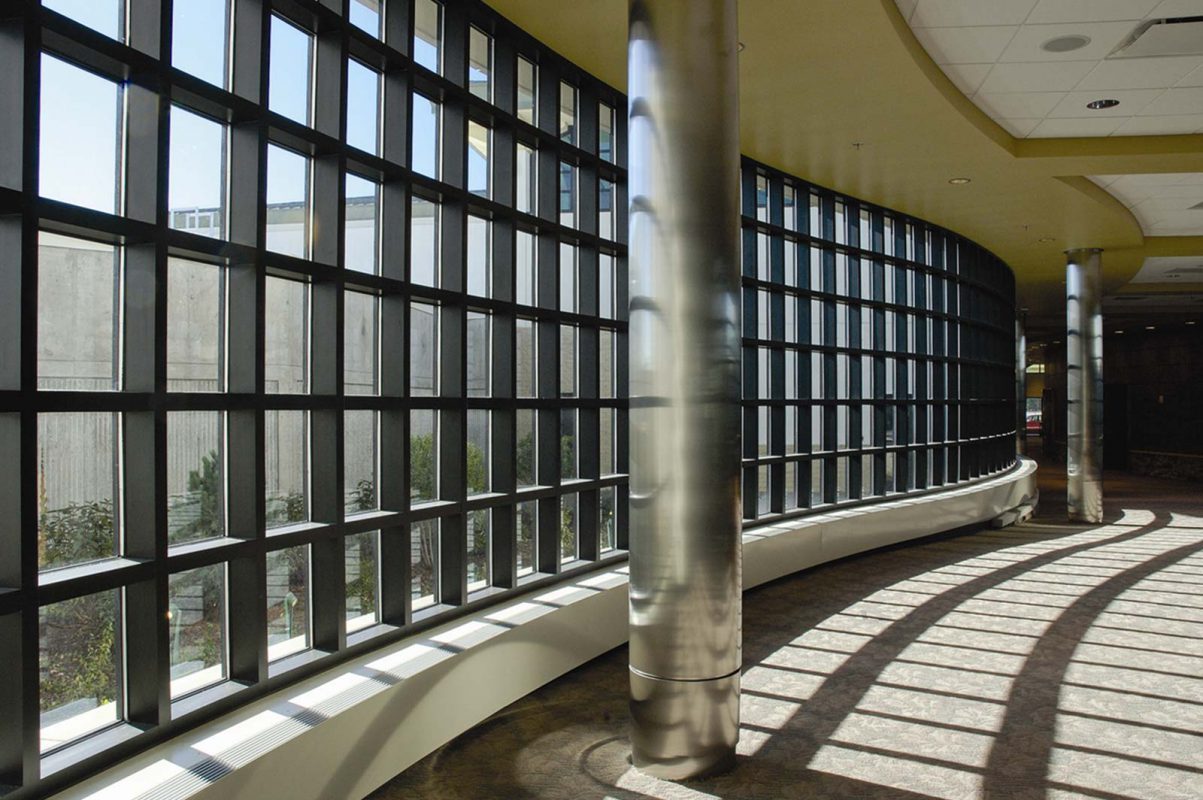
Eco-friendly anodize
As a result of industry demand for better aesthetics and sustainable design goals, Linetec converted it’s process to eco-friendly anodize. Linetec’s eco-friendly anodize offers LEED credit potential
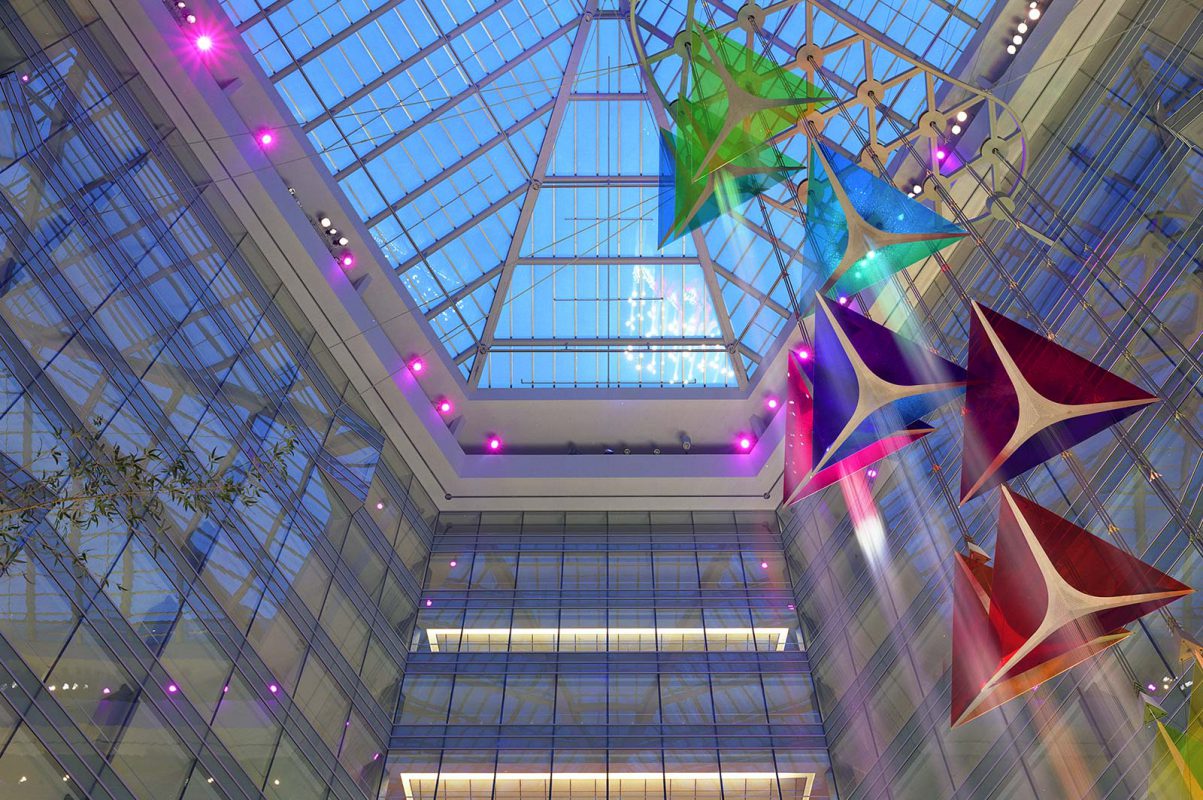
PVDF Resin-based paint coatings
PVDF Resin based (often referred to as Kynar 500®) coatings have been the proven mainstay in the architectural industry for decades. Linetec captures and destroys the VOCs present in liquid solvent-based paints at the factory before arrival on the building site.
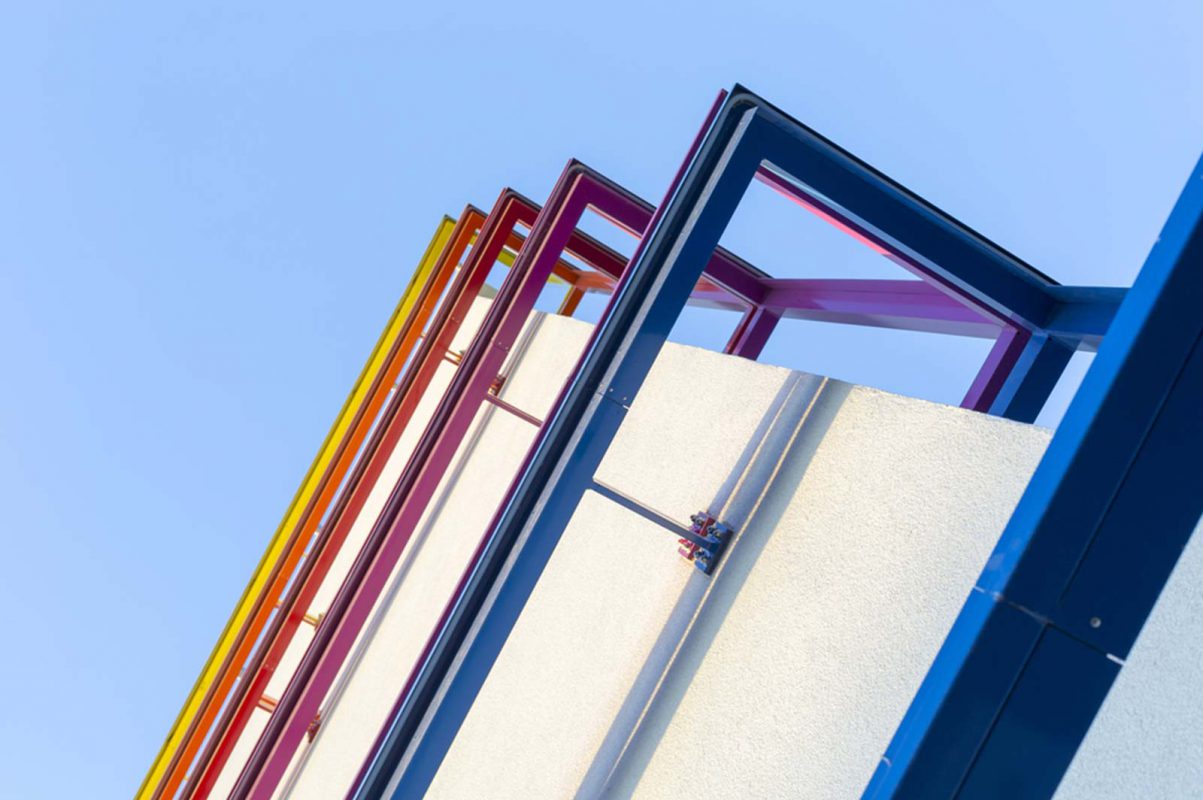
high performance powder coat
Powder coatings emit ultra-low levels of VOCs during manufacturing and application. They have a well-earned reputation for hardness and durability. The powder coat industry has made steady advances in technology to reach architectural performance standards.
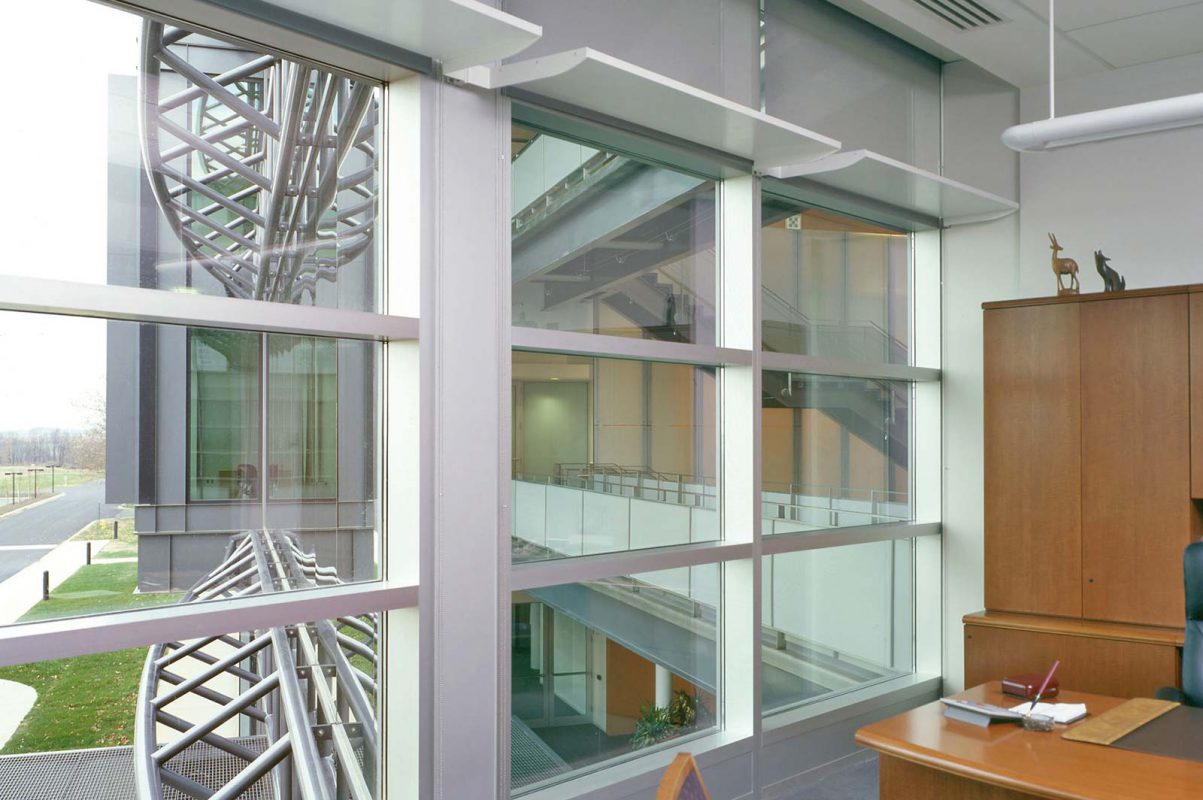
thermal comfort
Linetec provides manufacturers with two options – pour and debridge and thermal strut – to achieve significant improvement in thermal performance of window, door and curtainwall systems. Both energy saving systems can contribute to earning performance points toward LEED certification.
AAMA Verified Component Licensee
American Architectural Manufacturers Association, a material-neutral organization, is the source of performance standards for the fenestration professionals of window, door, skylight, curtain wall and storefront manufacturing companies.
LEARN MORE
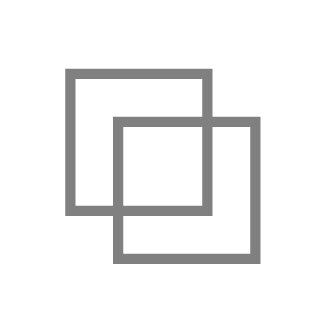
SPECIALTY FINISHES
As your Single Source Solution we offer custom options and specialty finishes such as Wood Grain Finishes, Copper Anodize, Spattercoat and textured Terra Cotta Coatings.
LEARN MORE
ENVIRONMENTAL COMMITMENT
Linetec has earned a long-standing reputation as a leader in environmentally-conscious practices and finishing options. For more than a decade, environmental responsibility has been written into our core values.
LEARN MORE
RESOURCE CENTER
Our technical experts at Linetec provide valuable industry education of high-performance architectural finishes to architects, engineers, specifiers and manufacturers.
LEARN MORE
Photo credits: Wausau Window & Wall Systems (Aaron Leitz Photography), Tubelite, Super Sky Products Intrl
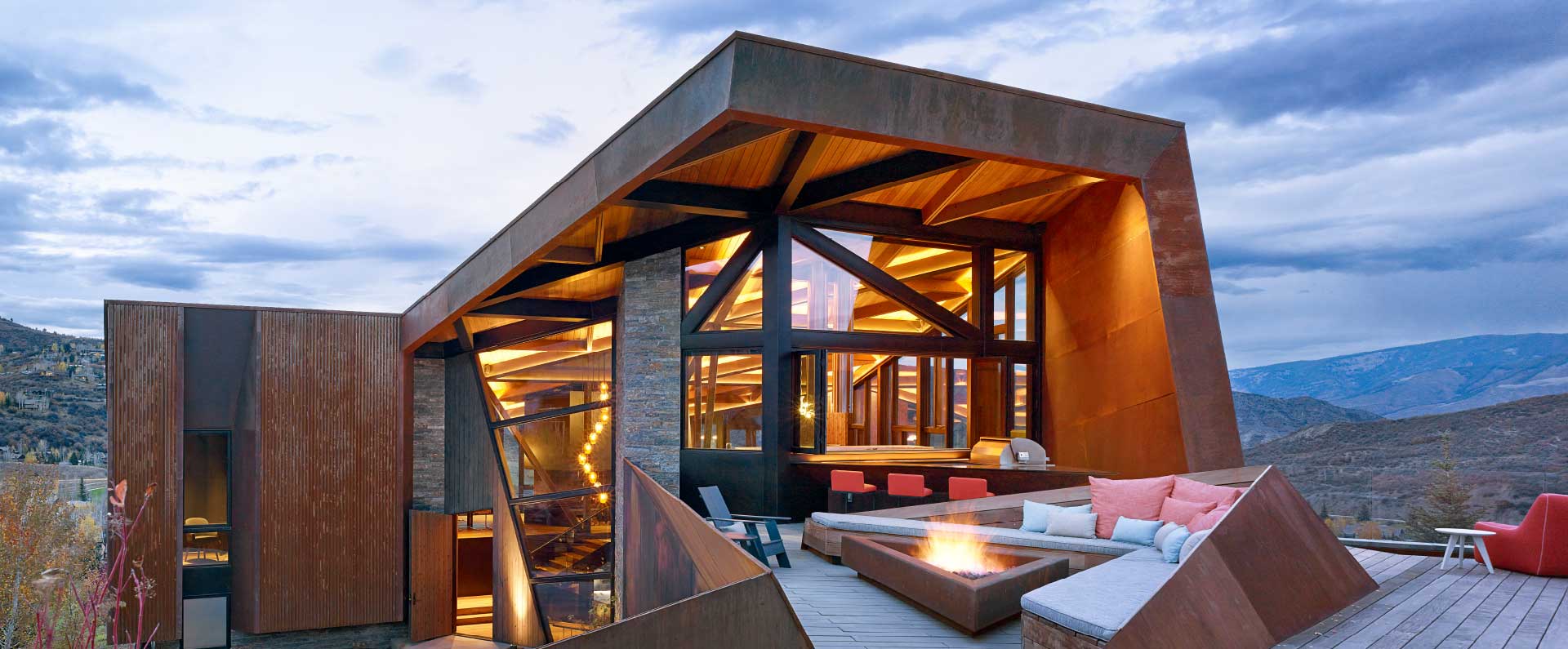
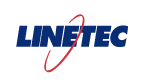
Architectural Paint
Architectural Paint Types
Color Charts
Request Samples
Request for Quote
PAINT SPECS & PROCESS
Linetec Paint Process
In-House Blending
Quality Control
Material Size Guidelines
AAMA Specifications
Warranty Information
Environmental Considerations
PAINT MAINENTANCE
ANODIZE FINISHING
Copper Anodize
Eco-Friendly Anodize
Anodize Color Samples
Request for Quote
Declare | Red List Free
ANODIZE SPECS & PROCESS
Anodize Process
Racking Methods
Quality Control
Material Size Guidelines
AAMA Specifications
Warranty Information
Environmental Considerations
ANODIZE MAINENTANCE
LINETEC SERVICES
Linetec Managed Inventory (LMI)
Stretch Forming
Linetec Trucking
Thermal Pour & Debridge
Thermal Strut
Brake Metal & Fabrication
Stock Flat Sheet & Extrusion
Packaging & Shipping
SPECIALTY FINISHES
Copper Anodize
Bordeaux Anodize
Wood Grain Finishes
Terra Cotta Coatings
Spattercoat
Request A Quote