When metallic paint coatings are applied to architectural aluminum products, the resulting finish provides a lively shimmer or sparkle with a vibrant, visual appeal. This attractive, modern aesthetic is produced by the way visible light reflects off the metallic flakes contained within the coating.
Metallic painted finishes protect the metal and enhance aesthetics of wall panel systems, canopies, sun shades, curtain walls, windows and entrances. Metallic coatings can make a memorable impression whether used throughout a project or applied on an aluminum feature wall, a main entry or a decorative accent.
Aluminum flake is used to create the popular sparkle. These metallic flakes can generate different looks depending on the paint production process, the paint line application techniques and the product’s final installation.
Optical dynamics
The light reflectance of the metallic flakes within the coating gives these finishes their lively appearance. The size and reflectivity of the flakes in the coating, their orientation and the degree to which they are all oriented in the paint coating will affect the brightness of the color. This is sometimes referred to as the “flop of the flake.”
Like tiny mirrors, the flakes that lie horizontal in the paint will reflect the most light. In an optimally applied metallic coating, the flakes are randomly oriented. This will achieve the greatest level of sparkle and depth.
If all the flakes in the coating were to lie horizontally, the maximum amount of light would be reflected. The surface would look very bright to the point of appearing almost solid rather than sparkling. If the metallic flake content is too high, the shimmer also is diminished and again, it will appear to be solid color paint rather than a metallic.
Taken to another extreme, if all the metallic flakes were to lie vertically in the paint, very little light will be reflected. The surface would appear very dark and possibly eliminate the coating’s intended brilliance.
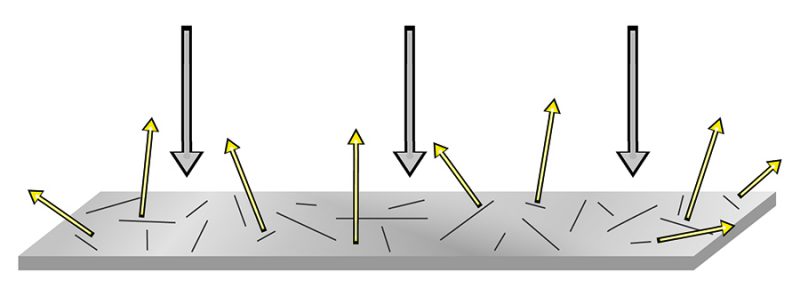
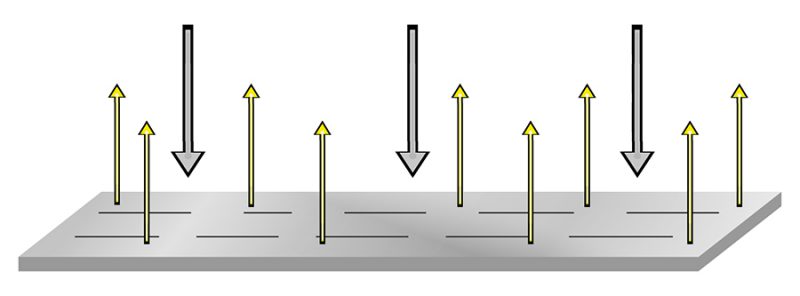
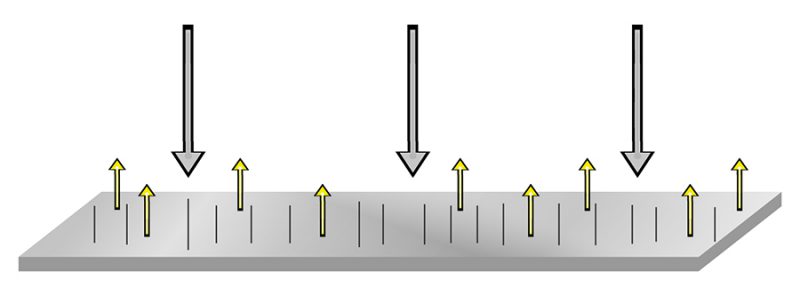
Optimal appearance
The same qualities that create the vibrancy and reflectivity of metallic coatings also can cause variations in appearance within a project, an elevation or even a single part of a metal building product. A project with lots of aluminum wall panels is more likely to show variation than one with extrusions or one with panels separated by masonry or other materials that disrupt the overall visual continuity of a building’s exterior. Always paint the same elevations and adjacent panels on the same application run.
Panels painted in a factory setting can appear visibly to match panel to panel on the paint line, but when installed, they can be perceived as non-matching under natural light conditions. The reflective properties of the metallic flakes mean that the same painted surface will look different throughout the day and year depending on the viewing angle, the angle of the sun or other light source as well as the intensity and type of the light source. Metallic painted aluminum panels also can appear to have a different color if they are not all installed on the same plane or are slightly warped.
Opportune outcomes
The differing sizes and geometries of brake metal, extrusion profiles and flat sheet parts are just some of the numerous variables that make it more difficult to apply a perfectly random flake orientation. Other aspects include:
- Different types of paint lines used by the applicator will affect the outcome of the painted finish.
- Different shapes of parts mean different painting distances from a part’s surface.
- Different application equipment will cause different flake distortion.
- Different pressures, atomization and human elements of supplemental hand-spraying with manual guns often will produce finishes that look different than an area sprayed with the accuracy of automated equipment.
- Different levels of electrostatic attraction within or between parts can occur.
- Different solvent types are used by different applicators to blend the paint.
- Different coverage should be anticipated for overlapping spray areas because these have twice the flake content as other areas.
Specify that all the paint is made in a single batch, especially when working on a large project or one with multiple phases. Similarly, when possible, indicate that a single finisher should apply the paint to ensure the greatest consistency and quality control. This will minimize the potential variation between different paint applicators and their different equipment.
Optional considerations
Some metallic colors have a greater propensity for visible variation. This can be particularly noticeable with bright, semi-transparent colors, such as silver metallics. When bright silver metallic coatings are specified, be sure to consult with the finisher to avoid unpleasant surprises and discuss alternatives, such as clear anodize. When a uniform aluminum alloy is specified, an anodize finish can enhance the metallic aesthetic and may have less visible variation than the flop of the flake phenomenon seen with painted metallic coatings.
As another, economical alternative to metallic coatings, mica paint coatings provide a similar appearance with slightly less brilliance or depth. These two-coat systems are manufactured with a non-conductive mineral rather than with conductive metal. Due to their inert formulation, they eliminate the need for a clear coat, are less sensitive to flake orientation and minimize visible variation improving the overall color consistency.
For personalized assistance with selecting metallic or mica coatings for your next project, please contact your local representative.