As you get closer to the coast, you can smell the ocean. Salt from seawater is sent airborne by breaking waves and picked up by the wind, scattering across coastal communities. In addition to the atmospheric odor, salt spray and deposits are among the main drivers of corrosion on exterior architectural aluminum components. This is because of salt’s chemical constituent chloride. It is not only beach-side buildings that suffer from salt exposure; significant airborne depositions of chloride from ocean spray have been found more than 50 miles away from the coastal shore.
Exposed, unfinished aluminum reacts strongly with chloride ions. Within weeks, the chemistry overwhelms the natural protective oxide layer and results in visible pitting. Prolonged exposure can compromise the structural integrity of aluminum components and lead to systemic failure of a building envelope. This effect is accentuated in industrial marine environments and coastal urban areas, where air pollution puts additional corrosive chemicals into the atmosphere.
Thankfully, reducing potential corrosion from salt spray can be mitigated by applying a high-quality, high-performance finish to aluminum building components.
Here are six important considerations when selecting a finish for architectural aluminum on projects near the coast:
1. Location
Coastal areas are especially aggressive outdoor environments for aluminum, and the closer you are to the ocean, the greater the concentration of salt in the air. Corrosion rates vary depending on temperature, wind direction, wave action, rainfall, humidity and the level of industrial air pollution.
Everchanging variables of a project’s climate make it difficult to predict the day-to-day conditions of a coastal area. Choose the most durable finishes for exterior architectural aluminum when a building is located near the ocean.
2. Fabrication
The shape and machining of an architectural aluminum product can affect how it responds to salt spray in coastal areas. Issues are more likely to occur at grain lines and flaws in fabricated metal. Seams, hems and cut holes and ends also are potentially vulnerable. For best results, remember to machine, bend and shape the metal before it is finished.
Once installed, any fabricated aluminum that holds moisture and prevents drainage also can create prolonged exposure to salinized solutions that may expediate corrosion. Be aware of concave components that can collect water, or insufficiently sized or blocked weepholes on curtainwall, storefront and window systems.
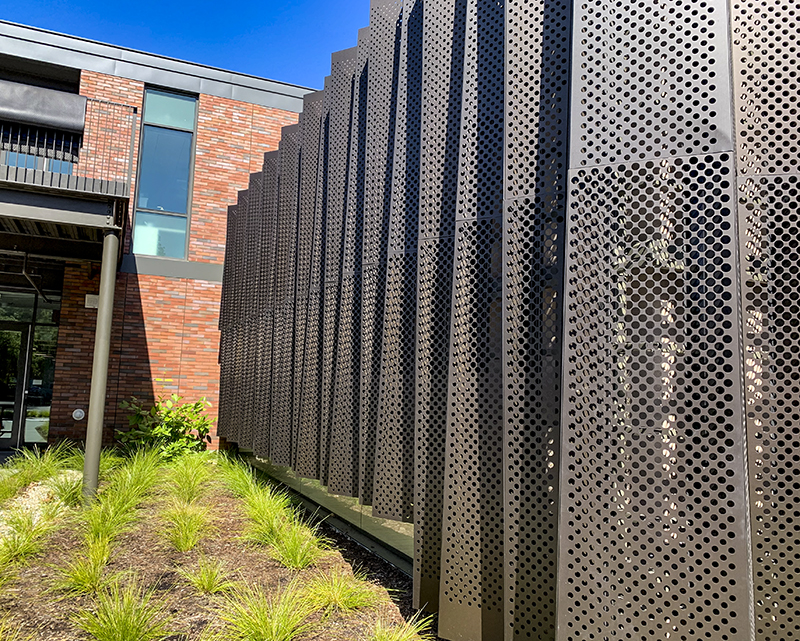
3. Paint Coatings
Paint allows for nearly unlimited color options, and when correctly specified, creates an outstanding high-performance coating for architectural aluminum components. To ensure longstanding durability against salt spray and coastal climates, select 70% PVDF resin-based architectural coatings to meet the Fenestration and Glazing Industry Alliance’s (FGIA’s) AAMA 2605 specification standard.
Finishes that meet AAMA 2605 exhibit exceptional durability and resistance to UV radiation, pollution and weathering. The rigorous testing of these PVDF coatings includes more than 4,000 hours of accelerated exposure to salt spray. In addition, 70% PVDF painted aluminum samples have been placed on an outdoor test site in South Florida. These test panels are monitored for adhesion, chalking, color fading and gloss loss under actual coastal conditions for years, even decades.
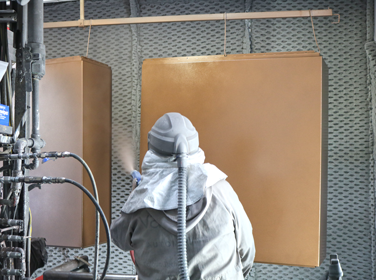
4. Anodize Coatings
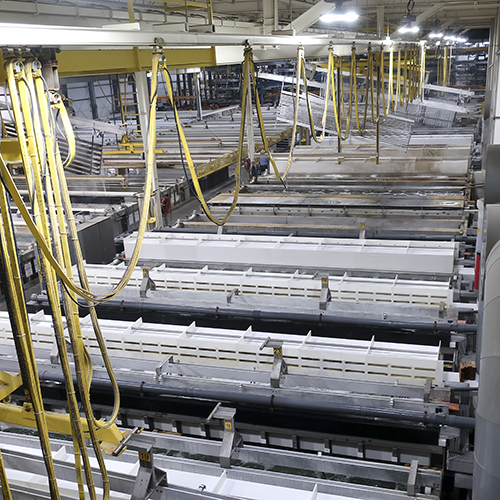
A Class I anodize coating that meets FGIA’s AAMA 611 specification provides another benchmark option for finishing architectural aluminum. Anodized aluminum that meets this standard are subjected to 3,000 hours of accelerated exposure to salt spray.
An extremely hard finish, anodize aluminum is ideal for high-traffic areas and challenging environments. Available is a range of natural metallic tones, Class I anodize coatings are an integral part of the aluminum substrate, providing excellent wear and abrasion resistance and shielding the underlying aluminum.
5. Maintenance
Even the most durable finishes need occasional maintenance, and cleaning architectural aluminum in coastal areas is the rule, not the exception. Regular cleaning helps remove accumulated deposits from salt spray, soil and pollution.
If your architectural aluminum is finished with a 70% PVDF coating or a Class I anodize, it should only require a rinse with clean water, or at most, a rub with a soft cloth and mild soap solution. It is important to avoid the use of strong alkaline or acidic cleaners and abrasive metal scarpers. These can damage the finish and expose the underlying aluminum to future salt-spray. When a finish is compromised, the negative affects to the metal substrate may become significant within weeks.
6. Finishing Partner
As a single source solution and experienced partner for architectural finishing, we understand that every one of your projects is important and those in coastal regions are no exception. With nearly 40 years of experience, Linetec’s associates deliver industry-leading reliability and exceptional quality for your finished aluminum products, and superior service to support you.
By choosing an experienced finishing partner, you can be assured that your finish meets the required specification and is supported with a long-term warranty. We offer standard warranties of five years for Class I anodize and 10 years for 70% PVDF coatings with an option to extend the length for qualified projects.
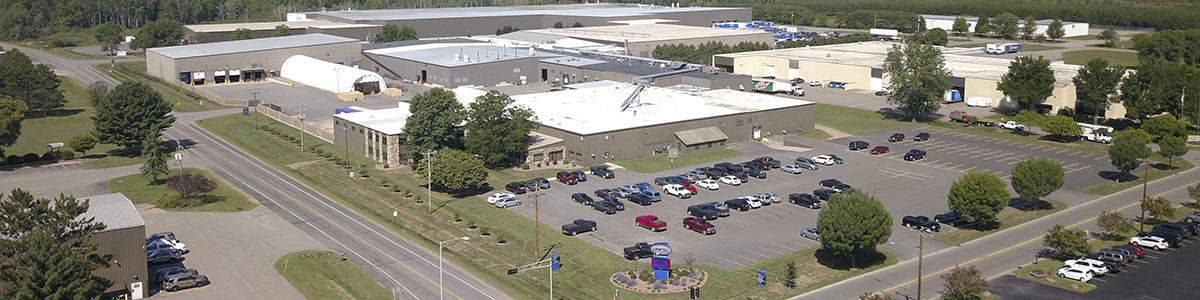
Please contact a Linetec associate serving your region for personalized assistance in selecting high-performance finishes to meet salt spray requirements for coastal projects.
Contact Us